Factory layout scan by drone: fast layout acquisition from air
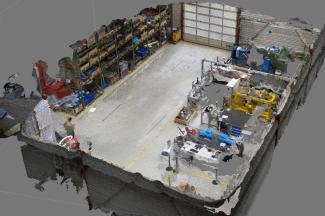
There is no faster way: Factory layouts can be captured in flight using a camera drone. The conventional method for capturing factory layouts involves measuring the entire factory manually, for example with laser measuring devices. How wide are the pathways? Where is which machine located? How much space does the warehouse need? Taking all these measurements and using them to create a detailed floor plan is very time-consuming and can take several weeks or even months.
To simplify this process, IPH offers drone-based 3D factory mapping for fast and low-effort data acquisition and analysis. This is done using a multicopter equipped with multiple cameras that generate 2D aerial images. Through the automated composition of the images (stitching/mapping) using photogrammetry, a true-to-scale 3D image of the factory can be generated automatically.
Factory layout capture from the air takes anywhere from a few minutes to a few hours, depending on the size of the factory. For example, capturing a factory of 5,000 m² takes about 1h. The acquired data can be used directly in the factory layout planning process, for example for room book generation as well as for the generation of digital 3D models or physical 3D-printed models. A digital 3D visualization of the factory from the obtained data offers, among other things, the possibility of a virtual tour through the current layout planning.
Companies need up-to-date, true-to-scale and detailed factory layouts especially when they want to restructure their facility and make it more efficient. Manufacturing facilities are constantly changing. Sometimes a new machine is added, sometimes the warehouse is expanded and sometimes workstations are relocated. As soon as it becomes too confusing or too cramped in the factory, companies should think about reorganization. This way, space can be regained - often without expensive extensions or new buildings.
The IPH supports companies in factory planning and reorganization. Since its foundation in 1988, IPH has been engaged in systematic factory planning based on the latest research findings and technology. Thereby, a holistic design approach is pursued with the aim of creating sustainable, scalable and adaptable factories. In particular, factory planning for Industry 4.0 is becoming increasingly important when it comes to achieving an increase in efficiency in production and logistics. IPH uses holistic approaches such as process analyses, manufacturing simulations and material flow simulations to review existing factory planning and to optimally design factory layouts and industrial architecture. Recently, factory layout capture by drone has also become part of IPH's service offering.